Mobile manipulators
Dual arm KELO 500
Bimanual manipulation in manufacturing and logistics
The dual arm robot is built on top of the base of a KELO DT 500. A torso with two light-weight manipulators replaces the vertical structure of the robot that accommodates various sensors and the haptic interface and is jokingly referred to as the “big O”. The robot is in the first place a research platform for studying motion coordination in assembly as well as in pick and place, or fetch and carry tasks. The bi-manual manipulation capabilities may be used in a variety of industrial applications such as bin picking in manufacturing, order picking fulfillment centers, or refilling shelves in a super market.
Technical specification:
- Drives: four 24V omnidirectional, inherently safe KELO drives
- Foot print: 65 cm x 65 cm
- Arms: 2 x 7 DOF lightweight arm
- Payload:
- Arms: 4 kg
- Platform: 250 kg
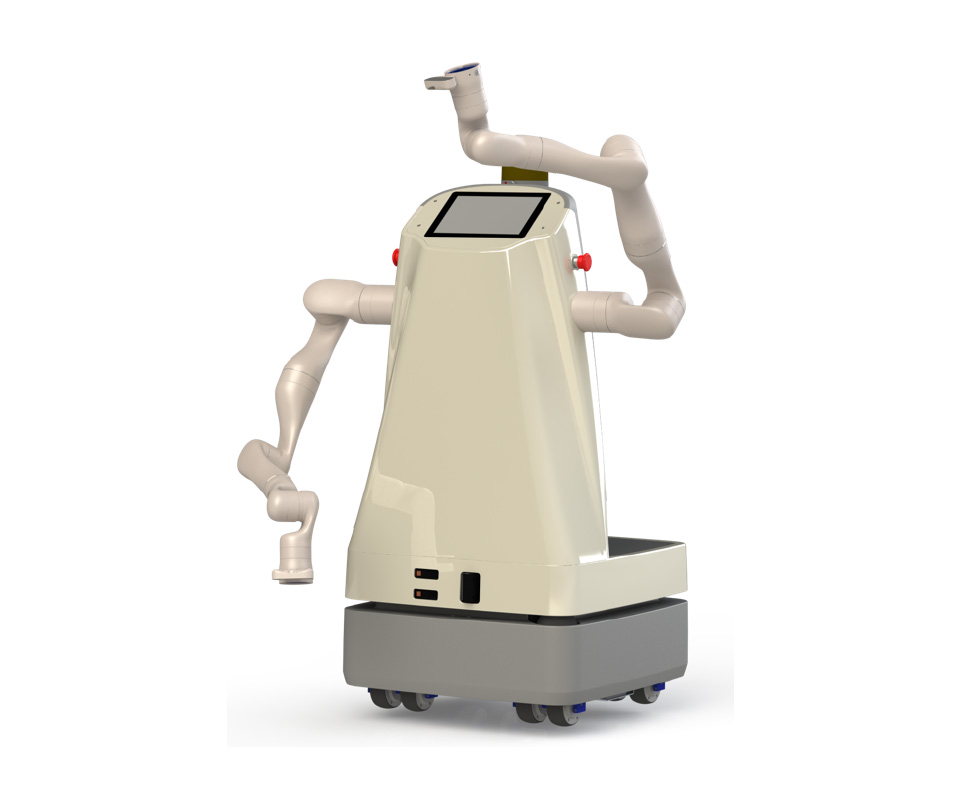
Manually operated robotic transport vehicles
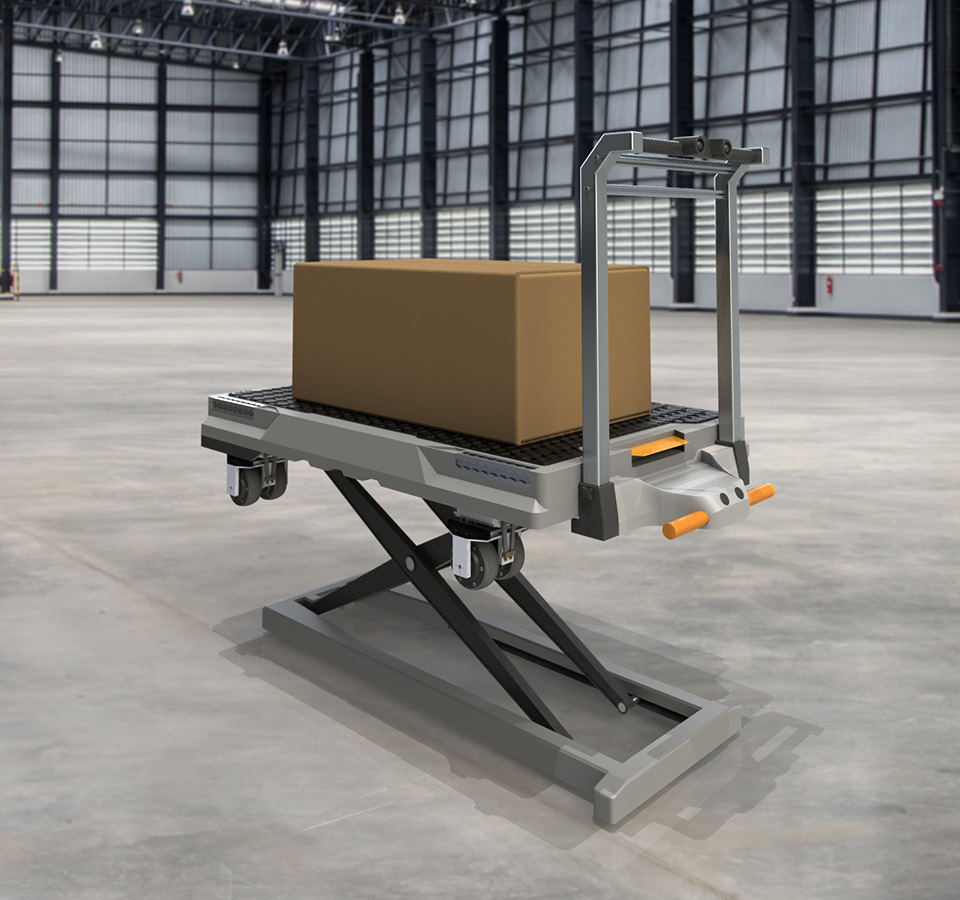
Roxetto
A robotized loading and transportation system
roxetto is a robotized version of the commercial loading and transportation system xetto ®. xetto ® is manually operated by a worker and can move and lift payloads up to 250 kg. While lifting is supported by a hydraulic scissor lift, moving the cart on ground requires manual labor and puts significant strain on the back of the worker. To reduce that strain roxetto is equipped with four KELO drives 100, which are controlled by a small embedded PC and act as force amplifiers. The original handle bar of xetto ® is replaced by a haptic interface, which senses the forces exerted on the handle. roxetto can be controlled with two fingers without causing any strain on the back of a worker.
Technical specification:
- Drives: four 24V omnidirectional, inherently safe KELO drives
- Loading platform: 118 cm x 68 cm
- Height of loading sill: max. 80 cm
- Lifting capacity: 250 kg
- Control: force-/torque sensitive haptic interface
A robotized material container
A manually operated robotic material container for mixed cargo
The robotized material container was designed to demonstrate the customizability and scalability of our platform concept. The container is equipped with 8 KELO drives 100, which together provide a payload of 1.000 kg. Like xettobot the container is equipped with a controller box, which accommodates an embedded PC. Attached to the container is force-/torque sensitive haptic interface, which was initially designed for roxetto. The sensor data from this haptic device are processed and interpreted by the embedded PC, which issues the necessary motion commands to move the container with minimal force
Technical specification:
- Drives: eight 24V omnidirectional, inherently safe KELO drives with special a seesaw suspension
- Container size: 300 cm x 200 cm x 200 cm
- Empty weight: 500 kg
- Payload: 500 kg
- Control: force-/torque sensitive haptic interface
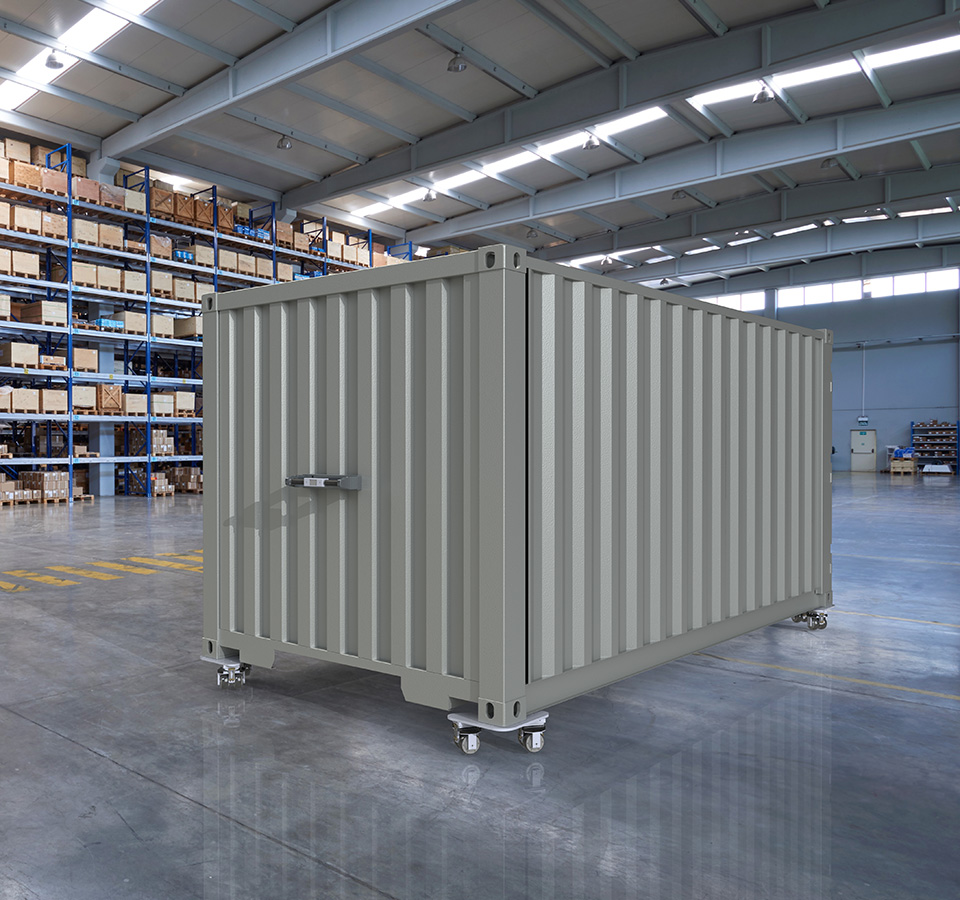